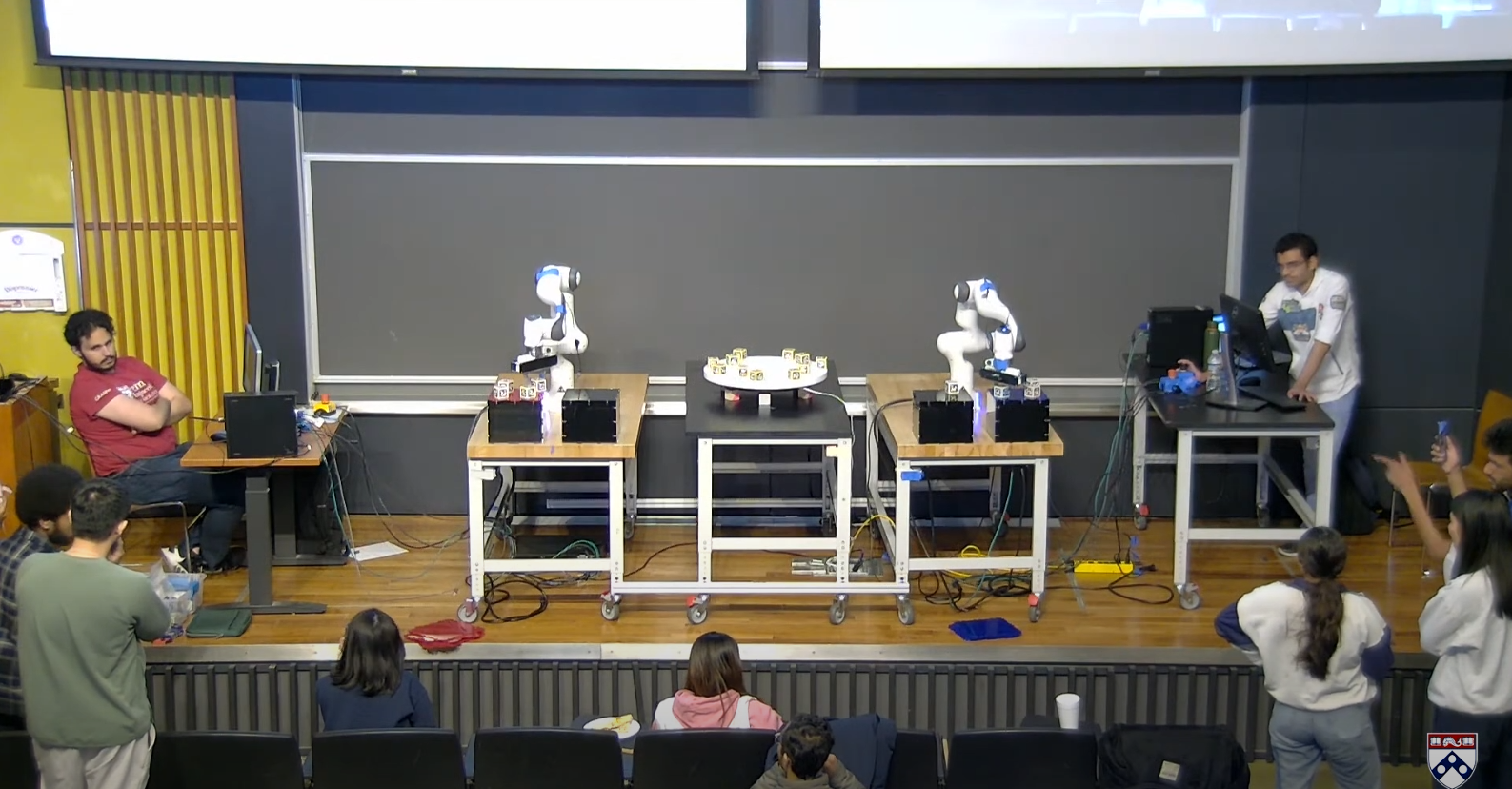
The project explored the capabilities of a robotic arm for grasping and stacking blocks under two primary scenarios: static blocks and dynamic blocks.
1. Environment and Set-up:
Simulation: Prior to real-world testing, the system's capabilities were analyzed in a simulated environment. This helped to predict the robot's performance, making it easier to identify areas of potential improvement.
Hardware Testing: After simulation, the arm's performance was tested in a real-world setup at the Robot Lab.
2. Static Block Stacking:
Detection & Orientation: The robot was designed to detect the blocks' location and orientation.
Grasping Mechanism: The robot's end-effector aimed to grasp the blocks at their centerline to achieve a straight stack.
Stacking Sequence: Post grasping, the robot placed the blocks on top of each other. It was noted that the end-effector sometimes bumped into blocks post placement, leading to misalignment.
Improvement Mechanism: To mitigate the collision issue with already placed blocks, an update was made to rotate the end-effector by 60 degrees after block placement.
3. Dynamic Block Stacking:
Transitioning: After stacking static blocks, the robot transitioned into a hovering position to deal with dynamic blocks.
Prediction & Timing: Given the blocks' motion, the robot had to predict the future position of the block and adjust its grasping timing.
Calibration: To optimize grasping, the robot's motion was calibrated with delays, based on block movement patterns on the red and blue sides.
Common Failures: Challenges in this approach included early or late reaching, incorrect orientation during grasping, and collisions with the moving blocks.
4. Analysis and Feedback:
Visualization: Videos were recorded during hardware testing to visually compare the performance differences between the simulated and real-world setups.
Performance Metrics: Key metrics such as success rate and completion time were used to gauge the robot's efficacy in block handling.
Overall, the robotic arm's method involved a combination of detection, orientation analysis, calibrated movement, and iterative feedback based on observed challenges and results. This multi-pronged approach ensured a structured mechanism to understand and improve the robot's stacking capabilities.
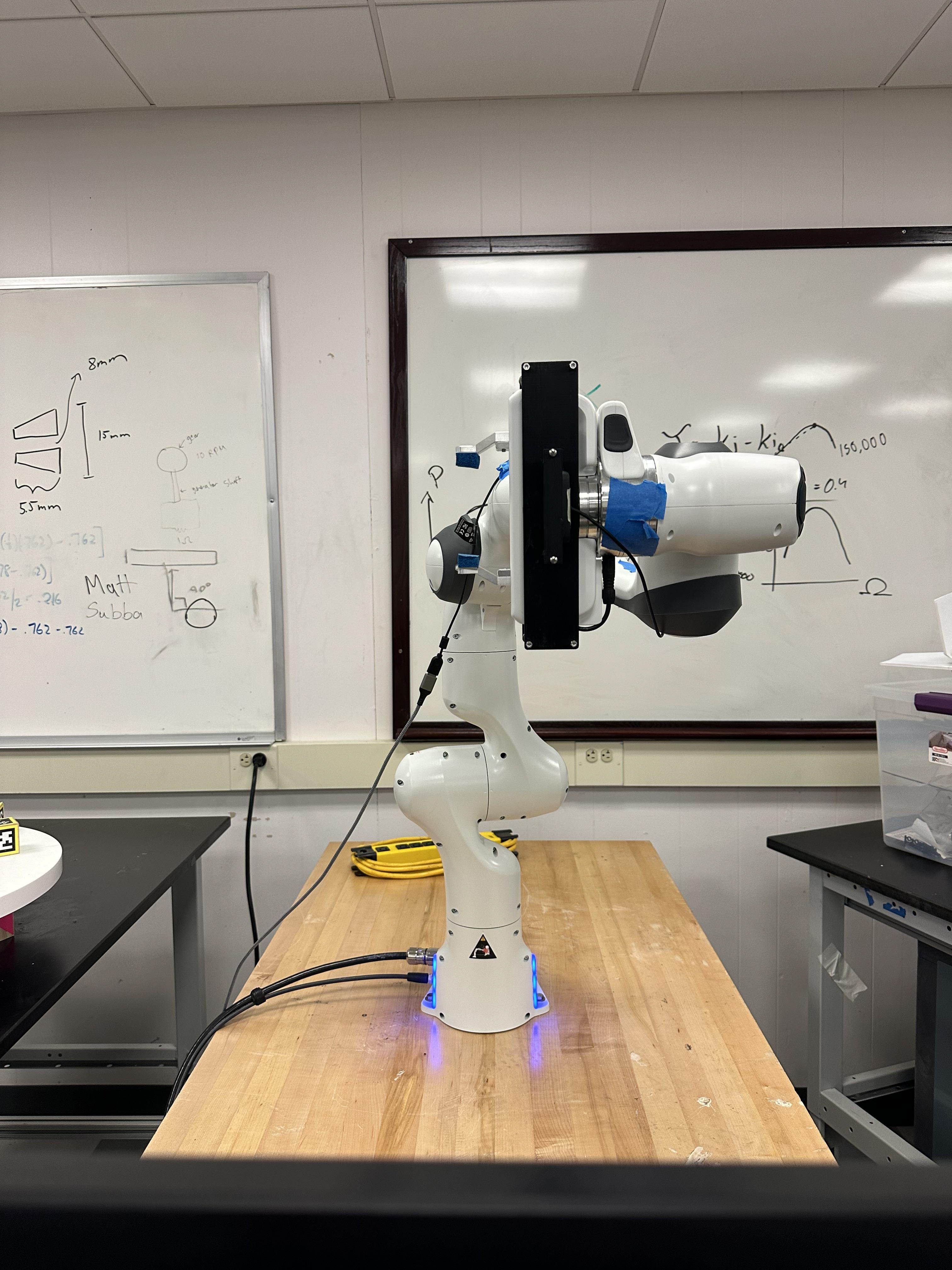
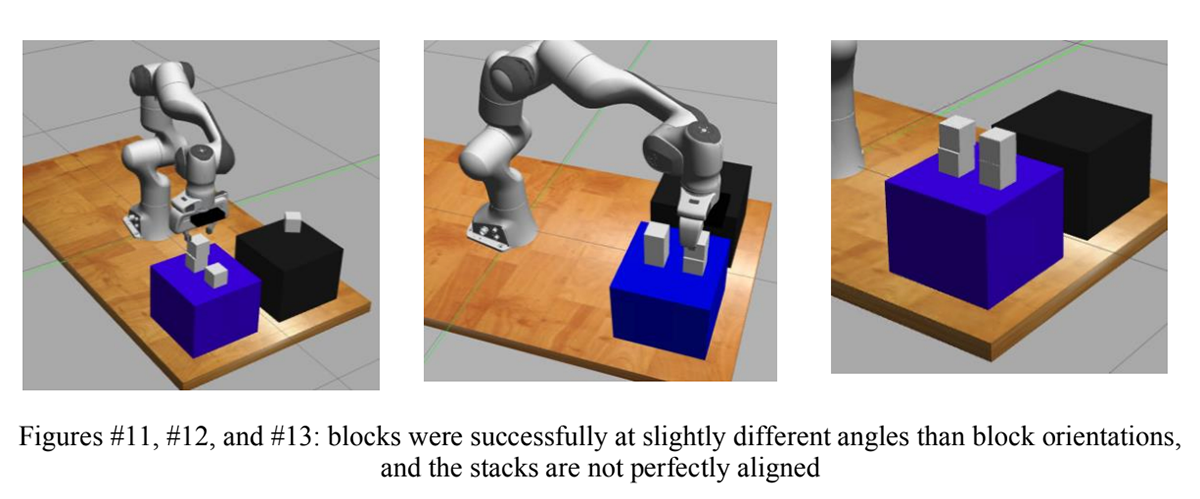
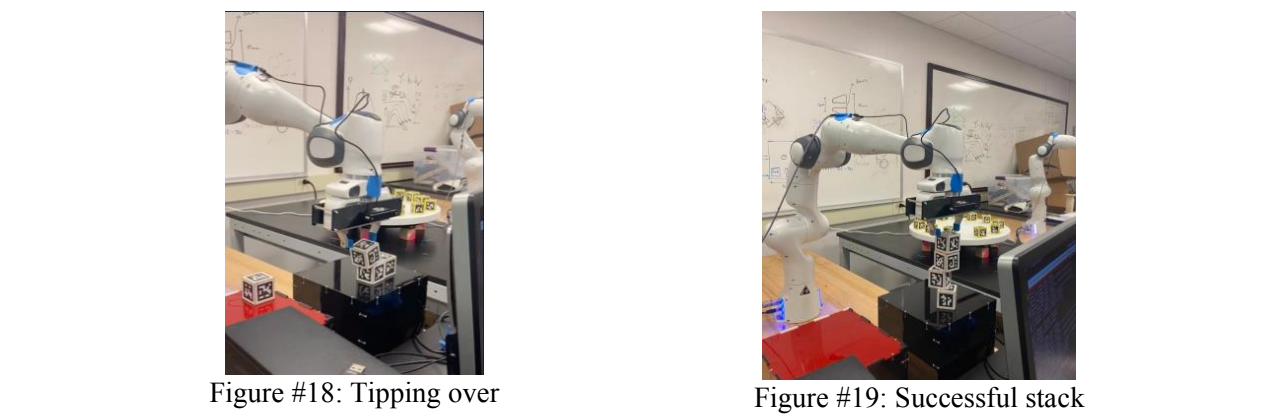